Comparing Thermal Efficiency: Polyamide vs. Polyurethane Thermal Barriers
The US Department of Energy reports that windows account for nearly 40% of energy loss in commercial buildings. To improve the overall energy efficiency of a building and adhere to increasingly stringent energy codes, the use of thermally broken aluminum window fenestration has become a standard practice. Thermal barriers play a crucial role in improving a building’s energy performance by preventing heat transfer through windows. While aluminum offers structural integrity, its high thermal conductivity necessitates the use of thermal barriers. This article delves into the differences between polyamide and polyurethane thermal barriers, two common materials used in fenestration.
Polyamide Thermal Barriers
Polyamide thermal barriers, also known as “struts” or “strips,” consist of rigid polyamide strips inserted into aluminum profiles. These pre-formed strips are crimped into place, forming a thermal barrier between the aluminum profiles. The polyamide strip system involves threading strips into the cavities of aluminum profiles after knurling machines add ridges to enhance adhesion.
Polyurethane Thermal Barriers
In contrast, polyurethane thermal barriers are poured as liquid polymer into aluminum cavities. Mechanical locks, such as abrasion hooks or lanced indentations, ensure adhesion of the polymer to aluminum. The liquid polymer solidifies within the cavity in less than 3 minutes. Finally, a strip of aluminum is “debridged” or removed in the bottom of the extrusion, forming a non-continuous aluminum profile. This construction enhances thermal performance by impeding heat transfer.
Comparison of Thermal Efficiency
Both polyamide and polyurethane barriers effectively reduce heat transfer through aluminum fenestration profiles. However, significant differences in material thermal conductivity ratings exist. Polyamide has a thermal conductivity rating of 2.08, whereas foamed polyurethane has a rating of 0.21 and solid polyurethane has a rating slightly higher than polyurethane foam. Lower thermal conductivity ratings indicate better U-factor and thermal efficiency, positioning polyurethane as the superior choice.
Strength and Durability
Polyurethane thermal barriers exhibit superior strength and durability compared to polyamide. In shear, tensile, and torsional strength, polyurethane outperforms polyamide by 4-5 times. This robustness is vital, especially in large fenestration systems like curtain walls, where the thermal barrier secures substantial glass panels in place. With a bond strength capable of withstanding 5000 pounds of force in a four-inch composite extrusion, polyurethane ensures long-term structural integrity.
Conclusion
In the realm of thermal barriers for aluminum fenestration, polyurethane emerges as the more effective choice. Its lower thermal conductivity rating and superior strength make it an ideal solution for enhancing energy efficiency and structural integrity in commercial buildings. Understanding the nuances between polyamide and polyurethane thermal barriers is pivotal for architects, engineers, and building professionals striving to optimize building performance and meet stringent energy standards.
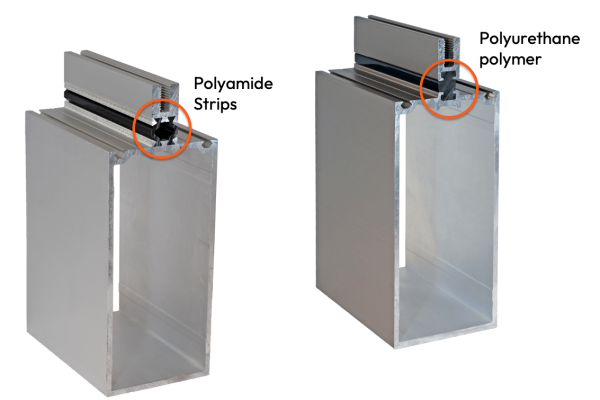